The solution to store, save and supply water
Saving water in dairies (part 2)
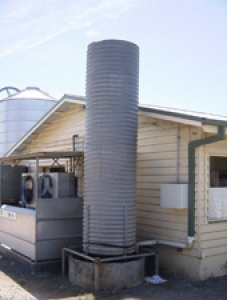
Part 2
Plate Cooler and Cooling Towers
Substantial amounts of water are used on farms to pre-cool milk. Typically farms use three times their daily milk volume each day for this purpose. Capturing this water and using it for another purpose is just one way to save water.
Check out the links below to find ways to save water when cooling milk.
- Optimise heat exchange - flow Rate / cooling Efficiency
- Curb operation of plate cooler water pump
- Tailor water to milk flow
- Recycle water for other dairy processes
- Store and re-use plate cooler water
1, Flow Rate / Cooling Efficiency
Description
Make sure the large volume of water used through your plate cooler is used wisely. Effective heat exchange will result in a small temp difference (within 20C) between incoming water and outflowing milk. How to check this.
Plate coolers need to be sized correctly for expected milk flow. Industrial plate coolers require less water (1.5-2 times milk volume) than the older ‘M’ types.
Tips on Getting the Best Result
Variable speed controllers on the milk pump (about $4,000) stabilise milk flow and make it easier to make good use of the water.
Pros and Cons
Efficient pre-cooling saves power and water but a clean, filtered water supply is needed.
Issues in Making it Happen
Labour
Time taken to dismantle plate cooler and clean it.
Milk Quality
Better milk cooling improves milk quality.
2, Curb Operation of Plate Cooler Water Pump
Description
Interlocking the plate cooler water pump and milk pump means that water is only moving through the plate cooler when the milk is.
This can be done manually – as a part of the start-up and wash routine.
Installing a relay switch from an ‘on-off’ controller on the milk pump will automate the process and should only cost an additional $300 - $400 on top of the price of a controller.
Tips on Getting the Best Result
Use coldest source of water available. Both milk and water inflows to the plate cooler need to be filtered.
Pros and Cons
Minimal effort required to save water. Less water going plate cooler may reduce water being pumped for another purpose (ie yard wash or stock water).
On-off switching may slightly increase wear and tear and energy load (especially if single phase).
Issues in Making it Happen
Labour
No issues if automated
Milk Quality
Care must be taken to not compromise plate cooler performance.
Tailor Water Flow to Milk Flow
Description
In sophisticated systems the variable speed control on the milk pump can also regulate the flow of water through the plate cooler – effectively tailoring the water flow to the milk flow.
Care is required here because the volume shifted by a pump is not linearly related to the speed of the pump, and so the water supplied to the plate cooler may be inadequate for heat exchange at times when the pump speed is low.
Tips on Getting the Best Result
Specifications for the variable speed controller and the ramifications for the water pump output must be known to ensure efficiency of pre-cooling. This is a job for the professionals as the pump speed, flow rates and plate cooler performance relative to milk pump flow rates must all be considered together.
Pros and Cons
Can improve milk cooling if set up correctly but often the information available to installers is based on the Australian standards (rather than the actual pump) so testing of the pumping efficiency must be done in situ.
Issues in Making it Happen
Milk Quality
Ensure adequate pre-cooling to reduce load on refrigeration.
Recycle Water
Description
Water can be diverted away from effluent and delivered for other purposes after leaving the plate cooler. Examples include – yard washing, use inside the dairy, for stock water or even as feed for hot water services.
Large volumes of filtered water are used daily so plate cooler water is well suited to recycling.
Tips on Getting the Best Result
Use hottest water to feed HWS (if from clean source). Make sure the flow rate of water going through the plate cooler is not reduced due to head or resistance created by down stream pipe work.
Pros and Cons
Uses plate cooler water pump for two purposes. May capture heat in water to lower power usage. Storage tanks are required.
Issues in Making it Happen
Milk Quality
Nil unless reduces pre-cooling efficiency.
Store and Re-Use Plate Cooler Water
Description
Water used through the plate cooler can be stored and re-used again and again if the heat is effectively removed.
Various system are available to remove heat from the stored water including natural draft and force draft cooling towers, heat exchange (through a body of water) and chiller units.
Commercial force draft cooling towers are very water efficient – cooling down a water store 3-4 times peak daily milk volume. Losses for this ‘closed loop’ system are less than 5%.
Tips on Getting the Best Result
Cooling towers work best in cool dry climates. Run the cooling tower at night when wet bulb temperature is at its lowest. Best on nights with low humidity.
Drift eliminators keep water losses from cooling towers to a minimum.
Pros and Cons
Can save water and reduce refrigeration costs.
Will reduce pre-cooling efficiency if no cooling tower. Cooling towers must be licensed in Victoria if tower incorporates a fan. M ay not be effective at certain times of the year (high ambient temperatures and/or high humidity).
Issues in Making it Happen
Labour
Some maintenance required for cooling towers. There are potential risks to people from Legionaries disease so their use is controlled in Victoria.
Milk Quality
Only a problem if reduces pre-cooling efficiency
To be continued

