Dairy farming
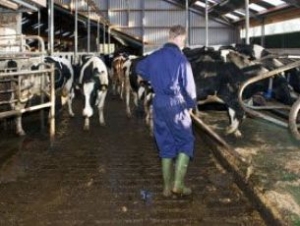
The fact that parlour renewal is a generational process, often occurring once every thirty years, is a problem that is restricting areas of the dairy sector from investing in the best automated parlour systems available at the present time.
Manufacturers are aware that without farm uptake, much development work on sophisticated energy saving machinery and computer monitored units is not put to best use.
Equipment like this lowers the amount of human variation and error seen across the farm and saves time, which according to Andrew Reece, DeLaval Managing Director of Great Britain and Ireland, is at the heart of 90 per cent of problems.
He says that the technology is available to make dairying work faster and better but the adoption rate is too slow.
“Of all the technology available I would say the Voluntary Milk System (VMS) is still in the earliest stages,” says Mr Reece. “It has been available for over ten years but DeLaval only came onto the UK market in around 2008 - this is an eight year adoption lag.”
He says that this is because producers had not been properly conditioned to want to buy it.
However, Mr Reece warns against haste as certain options will not work on specific farms. He also recommends proper assessments are made to ensure foot traffic is optimal before going to the trouble of installing VMS.
“It is very important that you have good cow traffic, a system that means a farmer is chasing cows is of little benefit. Station layout in relation to loose housing is critical.”
More importantly, Mr Reece advises that a farmer wishing to install VMS must be computer literate if the herd management benefits of the system are to be captured.
Under VMS herd staff no longer get the opportunity to stand next to each cow and assess for feet and udder ailments. This means farmers go from standing next to the cow two or three times a day, to a situation where visual inspections are done from greater distances.
For example, a mastitis case can be identified in an animal by the computer and the cow can then be diverted into a sick pen, explains Mr Reece.
“Farmers now have to rely on a PC to tell them what is right and wrong and if a farmer is not that way inclined then the facilities will not provide the greatest benefit.”
Just like a pilot driving an aeroplane, Mr Reece says that dials and alarm lists need to be relied upon to inform stockmen of health issues.
Mr Reece says that installation cost is the primary obstacle to defeat when selling farmers machinery. This can be overcome by clearly explaining the time and cost saving benefits of customisable cleaning systems.
“Many cleaning systems are now control-led on water temperature, detergent quantity, mechanical force and cleaning duration to tailor the wash action for a dairy’s unique requirements,” he says.
This allows for time savings of up to 60 per cent and water and detergent savings of over one fifth.
What’s more, all that is required is a push button and the operator can walk away and do other tasks, whether this is feeding animals or getting breakfast, adds Mr Reece.
“It is the same with VMS, all a farmer has to do is monitor the computer and look for alarm lists that will be generated hourly or daily and assess which cows have been milked and how many times.”
Other energy saving options include slowing the vacuum pump and letting it idle in the milking machine when it is not in use.
“Say a milking cycle lasts three hours – whenever a unit is taking off the udders and is not being used, the vacuum pump slows and lowers energy use,” explains Mr Reece. "This saves power compared to typical units that do not idle and run full speed for the duration of the milking process."
Milk pre-coolers are also available that lower milk temperature before it enters the cooling tank.
From the teat, the milk is around 35 degrees Celsius but can be intercepted with piped water cooling the milk to 20-25 degrees Celcius, reducing the energy requirements of the milk tank.
In winter, less water is needed to create a chill effect as the water may be 5-6 degrees, says Mr Reece.
Overall, Mr Reece maintains that the specific requirements of each holding have to be understood to provide optimum cost saving benefits and that some systems will suit some farmers more than others.

